Design for manufacturing (macro)
Jan 2021 | By: Thuan
There’s a common saying in project management, engineering, manufacturing: “time, cost, quality - choose 2”. This is obviously an oversimplified model of project constraints & management, but it is quite commonly used since it is very adaptable and easily communicated. The triangle (shown from Wikipedia) is commonly used to communicate that any changes in one constraint results in a trade-off against the other two. This is used to make decisions about what constraints are fixed and how to make trade-offs during both the design and implementation stages of a product.
A product can (and should) be intentionally defined by the appropriate metrics across all three dimensions.
Product (scope/quality): includes feature set, materials, consistency, aesthetic, manufacturing processes, assembly processes, technical specifications / requirements
Cost: includes cost of manufacturing, assembly, design / development, and as a result, the price that the consumer pays
Time: includes time to design & develop, time to manufacture & assemble, and as a result, time to delivery to customer
The reality is that, every company has to deal with these three constraints and makes decisions that affect them across the three dimensions — whether they realize it or not. I’m going to focus on hardware products since I think the battle there is even tougher once you start dealing with trying to maintain schedule, cost, and quality at scale.
Successfully designing a product with the right specs and features is tough, but only half the battle. The remaining half is implementation — manufacturing and delivering at scale is an often times underestimated enterprise.
While there are many crowdfunded products and group buys that are successful, there are many that are not because they fail to recognize and prepare for the very difficult problems associated with scaling. Delivering thousands of something is literally orders of magnitude more difficult than making tens of something. If not properly scoped and planned for, projects oftentimes result in higher pricing, much longer than expected lead times, and lower quality/feature set than originally designed for.
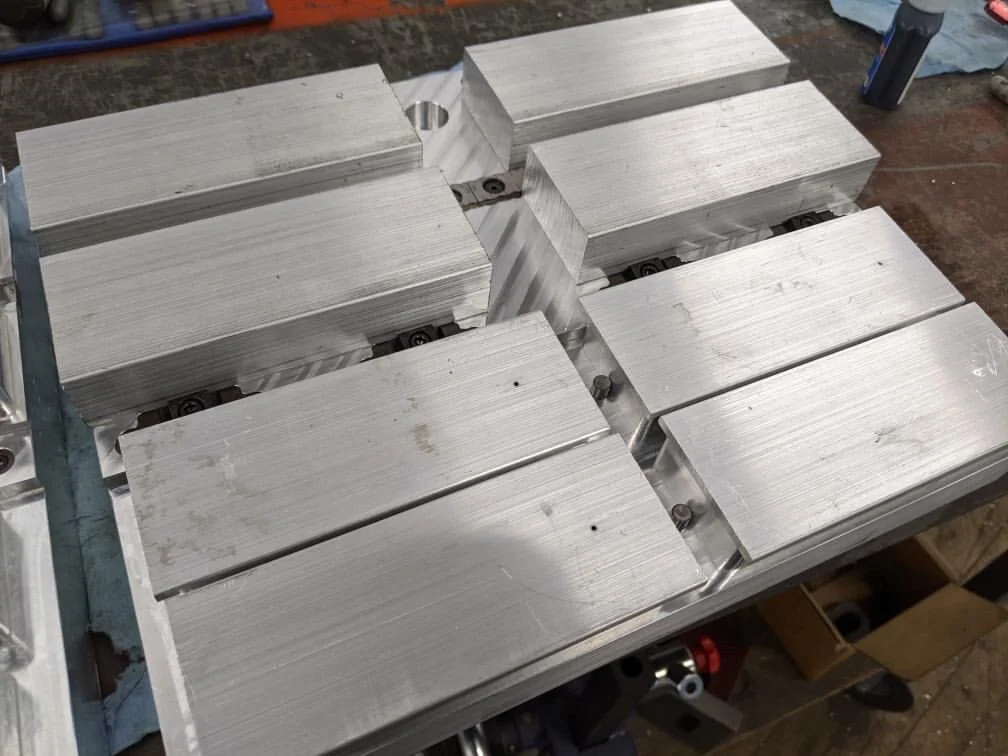



Thought experiment:
Think about making 1x - 10x units of a product — which is made much easier nowadays due to lower cost in 3D printing and other rapid prototyping techniques. The processes used might be time consuming on a per unit basis, but products can essentially be hand-made and hand-worked to get the final product ready. Little inconsistencies can be resolved relatively easily due to the nature of how the products are being made.
How does this process change if its thousands of units of a product? The same assembly/manufacturing processes become a lot more cumbersome in terms of time, effort, and consistency. Other manufacturing/assembly methods would be considered. The design & architecture of the product must accommodate for manufacturing, quality, and assembly.
Whereas before, a 10% failure/inconsistency could result in maybe 1 unacceptable part that could be identified and fixed, now it could result in hundreds of inconsistent parts
To address these quality issues, maybe the same product would require some optimization of design, fixturing, experimentation, etc. All this requires intentional planning/design from the beginning otherwise it results in higher cost, longer lead times, and/or worse quality.
As you can see from the pictures above, David and I opted to go with a design that utilizes a machined housing w/ plate mounted switches (not always the best solution for scaling). There are product decisions that we could have made to make it better for scale including using different materials / different manufacturing processes (ie: 3D printed, sheet metal, PCB mounted switches, etc), but we decided that this was the quality/scope we wanted, and defined the timing and cost from there. We’ve made intentional design decisions to help optimize such a design for cost & timing:
designing parts to minimize number of separate operations and minimize number of setups
additional timing for the manufacturer to create fixturing
working with our vendor to better define finishing + anodizing processes to improve consistency
cost + timing planning to allow for rejections of parts due to any finishing inconsistencies (between media blasting and anodizing the parts)
So what happens if it turns out that despite all our effort, we only sell 10 units? Well then, all that effort and planning for scale was just a good engineering exercise. However, in the event that we have to scale to orders of magnitude beyond that (*fingers crossed*), we are confident that we’ve properly (and intentionally) defined a scope of product and quality of product that can be delivered within the cost and time frame that we’ve planned for. In other news, we’re extremely excited to get this run of parts in!